EVA (ethylene vinyl acetate copolymer) foam is ubiquitous in modern industry and everyday life. From soft cushioning in the soles of athletic shoes, to delicate packaging linings in electronics, to comfortable soundproofing components in automotive interiors, EVA foam plays an important role with its unique properties.
EVA is a thermoplastic elastomer made by polymerizing ethylene and vinyl acetate under high temperature and pressure. The content of vinyl acetate (VA) is a key factor in determining the performance of EVA materials; when the VA content is low, EVA materials are closer to polyethylene, with better rigidity and tensile strength; with the increase of VA content, the elasticity, flexibility, transparency, and low-temperature resistance of EVA materials are gradually improved, and the compatibility with other materials is also better. EVA materials with different VA contents are suitable for different application scenarios, which also provides the basis for the diversification of EVA foamed products.
Physical foaming
The core of physical foaming is to utilize the dissolving and releasing properties of low volatile liquids or gases in EVA. In the production process, low volatile liquid or gas is first dissolved into EVA under certain temperature and pressure to form a homogeneous system. When the temperature of the system is lowered or the pressure is reduced, the liquid or gas originally dissolved in the EVA is rapidly released to form gas bubbles, thus causing the EVA material to expand and foam.
Temperature and pressure are the key controlling factors in the physical foaming process. If the temperature is too high, the gas or liquid evaporates too quickly, which can lead to uneven bubble sizes and ruptured pores; if the temperature is too low, the foaming process cannot be triggered effectively. Pressure control is equally important. The right pressure ensures that the gas or liquid is uniformly dissolved in the EVA, while the speed and degree of pressure release directly affects bubble formation and the structure of the foam. For example, the slow release of pressure can make the bubble gradually expand, the formation of a more uniform pore structure; rapid release of pressure may produce larger bubbles and irregular pores.
Physical foaming method has the advantages of relatively simple operation, high production efficiency and environmental friendliness, etc. It is commonly used in the production of EVA foamed products with relatively less demanding requirements on bubble structure, such as some common packaging materials, toy foams and so on.
Chemical foaming
Chemical foaming is a chemical reaction that generates gases that cause the EVA material to expand and form a porous structure. This method requires the addition of a variety of auxiliary agents, such as blowing agents, catalysts, stabilizers, etc., to the EVA raw material.
The blowing agent is the key component of chemical foaming. The commonly used AC series blowing agents (e.g. AC-3000) are high-temperature blowing agents with a decomposition temperature of over 220 degrees. Under high temperature and high pressure, the blowing agent decomposes rapidly and produces a large amount of gases, such as nitrogen and carbon dioxide, etc. These gases form pressure inside the EVA material, causing it to expand and foam.
The role of catalysts is to reduce the decomposition temperature of the blowing agent and accelerate the chemical reaction rate, thereby improving production efficiency. For example, zinc oxide reduces the decomposition temperature of AC blowing agents to about 160 degrees, allowing the production process to be carried out at more easily controlled temperatures.
Stabilizers help control bubble stability and prevent foam shrinkage. During the foaming process, after bubbles are formed, without the stabilizers, the bubbles may rupture or shrink due to internal pressure changes, surface tension, and other factors, affecting the quality and performance of the EVA foam. Stabilizers through the formation of a protective film on the surface of the bubble, enhance the stability of the bubble, to ensure that the foam has a good pore structure and physical properties.
Chemical foaming method can accurately control the foaming process, the production of EVA foam products with a specific density, pore structure and performance, suitable for product quality and high performance requirements of the field, such as sports shoes, automotive interiors and so on.
Analysis of EVA foaming formulation
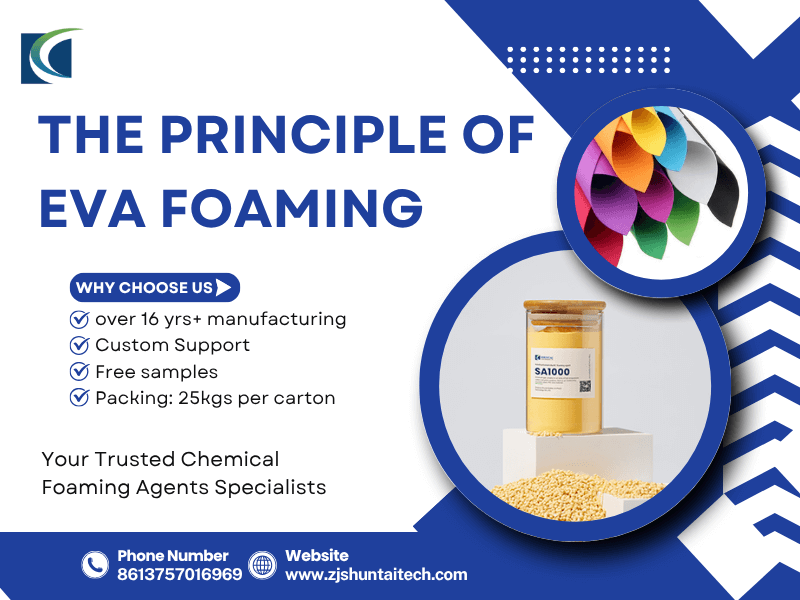
EVA foaming formulation is an important factor in determining the performance of EVA foamed products, which generally consists of a variety of raw materials such as the main material, filler, blowing agent, bridging agent, foam accelerator, lubricant and other raw materials.
Main material
The main material is usually EVA or PE, and other materials such as rubber, POE (Polyethylene Octene Co-Elastomer), TPR (Thermoplastic Rubber), etc. can be added according to the performance requirements of the products, and the level of VA content in EVA almost directly determines the performance of the EVA foamed products. For example, EVA material with higher VA content has better flexibility and elasticity after foaming, which is suitable for making products requiring good cushioning performance such as sports shoe soles, while EVA material with lower VA content has higher hardness and rigidity after foaming, which is suitable for making some packaging materials requiring support and protection.
In actual production, the choice of the main material and the proportion of the main material needs to be considered in the application of the product, performance requirements and cost and other factors. For example, for some cost-sensitive general packaging products, PE may be more often used as the main material; while for high-end sports shoes, a specific VA content of high-quality EVA material will be used, and POE and other auxiliary materials are added appropriately to enhance the performance.
Fillers
Currently, calcium carbonate and talc are commonly used fillers in EVA foaming. The main functions of fillers include reducing costs, increasing product rigidity and, to a certain extent, providing thermal conductivity. By adding fillers, the amount of main material can be reduced, thus lowering the production cost. At the same time, the addition of fillers improves the hardness and rigidity of the EVA foamed products, making them more suitable for applications that require support and protection.
The particle size of the filler is an important indicator of its quality. Fillers with smaller particle sizes are better dispersed in the EVA material, which improves product properties more uniformly and avoids product quality problems caused by filler agglomeration. In actual production, it is necessary to select the appropriate particle size filler according to the specific requirements of the product.
AC series blowing agents are the most commonly used blowing agents in EVA chemical foaming. These blowing agents have the advantages of high decomposition temperature, large gas production and stable foaming effect. Take AC-3000 as an example, it decomposes rapidly at a high temperature of more than 220 degrees Celsius, generating a large amount of gas, which makes the EVA material expand and foam.
The amount of blowing agent has a significant effect on the density and performance of EVA foamed products. If the dosage is too much, it may lead to excessive foaming, low density of the product, unstable structure of the bubble holes, or even rupture of the bubble holes, etc. If the dosage is too little, the foaming will be insufficient, the density of the product will be too high, and it will not be able to meet the expected performance requirements. In the actual production, according to the type of the main material, the proportion of the formula and the production process and other factors, precise control of the amount of blowing agent.
Bridging agent
Bridging agent (cross-linking agent) plays a key role in the EVA foaming process, it can make EVA molecular chains form chemical bonds between the material to improve the strength, heat resistance and chemical stability of the material.DCP (di-sec-octyl phthalate) is the most widely used bridging agent at present, and its half-life at 180 degrees is 1 minute, and at 130 degrees the half-life is 10 minutes. Therefore, in order to avoid premature decomposition of DCP in the mixing process, the temperature is generally controlled below 120 degrees.
For some products with special requirements on odor, BIPB can be used as a bridging agent, and used in conjunction with TAIC. Different production processes have different requirements for the amount of bridging agent, in flat foam and in-mold small foam, the amount of DCP is generally 0.5 - 0.6Phr; while in the injection foam, due to the process characteristics and the requirements of product performance, the amount of DCP is generally 0.8 - 1.0Phr.
Foaming accelerator and lubricant
Foaming accelerator can speed up the decomposition of blowing agent, improve the foaming efficiency, make the foaming process more uniform and stable. In the actual formulation, usually according to the type of blowing agent and production process requirements to choose the appropriate foam accelerator.
The function of lubricants is to reduce the frictional resistance of EVA materials during processing, improve the fluidity of the materials, prevent the materials from sticking in the processing equipment, and improve the production efficiency and product quality. Commonly used lubricants include stearic acid and its salts, etc., which can form a lubricant film on the surface of the EVA material, reduce intermolecular friction, and make the material easier to process and mold.
Factors affecting the quality and performance of EVA foaming
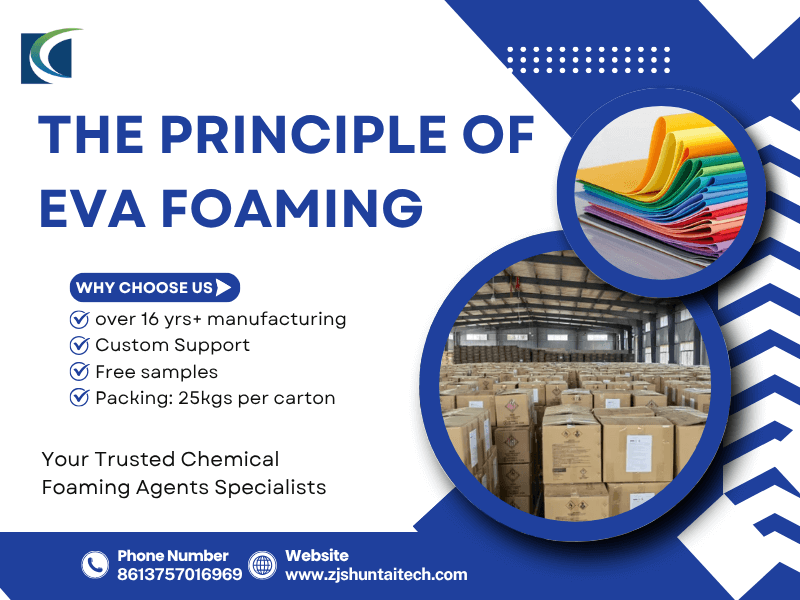
In the EVA foaming process, the quality and performance of EVA foam are affected by a combination of factors.
Raw material factors
The type of raw material, VA content, and the quality and proportion of other auxiliary materials directly determine the basic performance of EVA foamed products. Different brands and batches of EVA raw materials may have different properties, which will have an impact on the foaming process and the quality of the final product. The purity, particle size, and decomposition characteristics of fillers, blowing agents, bridging agents, and other raw materials also affect the foaming effect and product performance.
Process factors
Temperature: Preheating temperature, foaming temperature and cooling temperature are critical to the EVA foaming process. The preheating temperature affects the mixing uniformity and fluidity of raw materials; the foaming temperature determines the decomposition speed of blowing agent and the amount of gas generated; the cooling temperature affects the final structure of the bubble and foam. Improper temperature control may lead to insufficient foaming, uneven bubble hole structure, product deformation and other problems.
Pressure: The magnitude of pressure and the process of pressure change affects the dissolution and release of gases in the EVA material. Appropriate pressure can ensure the uniform formation and stable growth of gas bubbles, insufficient pressure may lead to gas bubbles can not be fully expanded, too much pressure may make the gas bubbles rupture.
Time: Process time parameters such as mixing time, foaming time and cooling time also affect the quality of the EVA foam. Mixing time is not enough, the raw material mixing is not uniform, affecting the foaming effect; foaming time is too short, foaming is not sufficient; cooling time is not enough, the foam structure is not stable, easy to shrinkage and deformation.
Applications of EVA Foam Material
With its unique properties, EVA foam is used in a wide range of applications.
Shoe Materials
EVA foam is used in a large number of shoe soles in sports shoes, casual shoes and other footwear products. Its good cushioning performance can effectively absorb the impact generated in the process of sports and reduce the injury to the feet and joints; its excellent elasticity makes the shoes more comfortable when walking and exercising; at the same time, the EVA foamed soles also have the characteristics of lightweight, wear-resistant and non-slip, which improves the overall performance of the shoes and the wearing experience.
Packaging field
EVA foam material has good cushioning, shock absorption and heat insulation properties, and is ideal for packaging of fragile items such as electronic products, precision instruments and glass products. Its soft texture can closely fit the product and provide all-round protection against collision and extrusion during transportation and storage. In addition, EVA foam has good chemical resistance and weather resistance, and can adapt to different environmental conditions.
Automotive
In automotive interiors, EVA foam is commonly used in seats, dashboards, door panels and other parts to provide sound insulation, vibration damping, heat insulation and decoration. It can effectively reduce interior noise and enhance driving comfort; meanwhile, its good heat insulation performance helps to maintain a stable temperature inside the car and reduce air-conditioning energy consumption. In addition, EVA foaming material can also be used for sealing and heat insulation of automobile engine compartment and other parts to improve the reliability and safety of automobiles.
Other fields
EVA foam is also widely used in toys, sporting goods, household products and other fields. In the toy industry, its safe, non-toxic, soft and elastic characteristics are loved by children; in sporting goods, it can be used to make yoga mats, sports protective gear, etc.; in household goods, it can be used to make floor mats, soundproof materials, etc.